Author
|
Message
|
Brent
|
|
Group: Forum Members
Last Active: 5 Months Ago
Posts: 142,
Visits: 1.5K
|
Hello, I have installed C4 transmission and 9” rear. The driveshaft U-joint angles are high, if I understand the concept correctly. Specs: Crankshaft/output shaft: .5 degrees down = 9 degree operating angle driveshaft: 9.5 down pinion: 1.5 down = 8 angle I have gathered that less than 3 degrees u-joint operating angle is desirable. At 9 degrees Spicer lists safe operating rpm to be 2000, the engine is built for 6000. The driveshaft is 31.5” long, using a right angle calculator, the rise is around 5”, to get to 3 degrees the rise must be around 1.5”, The T-bird x-member frame and distance to the pinion make this seem impossible to me. I could raise the pinion .5” more, but that does little to the operating angle. I believe the T-birds have a steep driveshaft angle from the factory; I did not measure the specs before I took it all apart, never considered driveline angles at that point. I never had a problem revving it up back when I drove it 35 years ago.
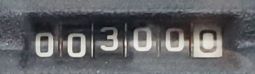 .150 Stroked Y-Block:327.25 ci @ >1hp per ci
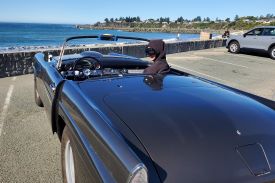
|
|
|
55blacktie
|
|
Group: Forum Members
Last Active: 13 hours ago
Posts: 1.2K,
Visits: 1.7K
|
I would check with Gene of Flat-O Products. Give him a call. I'm doing the C4 conversion in my 55 T-bird. I would think that there should not be an issue when keeping the original engine and rear axle, and you have not severely changed the ride height.
Let us know how it turns out.
|
|
|
Brent
|
|
Group: Forum Members
Last Active: 5 Months Ago
Posts: 142,
Visits: 1.5K
|
I used the Flat-O adapter and mount, two extra holes drilled center of stock transmission support and the C4 mounted perfectly. I used a RobMC starter to work with the FPA headers. I did add a new Ford 9" rear end but as I mentioned, if I understand the driveline angle concept, the geometry of the T-bird (transmission tail shaft sits close to the x-member and the driveshaft is short.) makes it a real question of how, to me. The C4 is in the same vertical position as the Fordomatic. I think, the T-birds are run with higher than optimal operating angles, stock. I'm hoping that some of the high performance Early Bird builders will enlighten us.
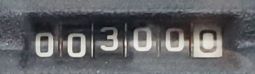 .150 Stroked Y-Block:327.25 ci @ >1hp per ci
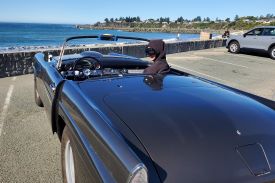
|
|
|
FORD DEARBORN
|
|
Group: Forum Members
Last Active: 9 hours ago
Posts: 769,
Visits: 113.4K
|
I have little experience with early Birds but seems that with a C4 the installation wouldn't be drastically different in terms of total engine transmission length. Not at all sure of that though. When visiting this on my '64 F100, I remember that it is desirable to maintain 3* or less at the u-joints and both need to be the same angle. Wedge shims can be placed between the leaf springs and spring pads for tweaking the angle. Drive shaft rpm is related to rear wheel rpm through the differential and when calculated at the expected max vehicle speed, I think the driveshaft rpm will appear to be more sane. Also, I bought a digital angle finder and found that to be very useful for dealing with this. I know there are many folks with more experience than I have on this subject who could offer more. Hope this helps, JEFF...............
64F100 57FAIRLANE500
|
|
|
Brent
|
|
Group: Forum Members
Last Active: 5 Months Ago
Posts: 142,
Visits: 1.5K
|
Thanks Jeff, The joints are within the, optimal, no more than1 degree difference. The transmission output shaft cannot be lowered or angled down anymore without cutting the x-member. The pinion can be raised (another .5" comfortably) toward the height of the output shaft thereby reducing the angle of the driveshaft and operating angles. But, if I have the calcs correct: The driveshaft is 31.5” long, using a right angle calculator, this equals rise of around 5” in the length of the driveshaft, to get too 3 degrees the rise must be around 1.5” meaning the pinion would have to move up towards the height of the output shaft approx. 3.5" I don't think that is achievable. One thought: If the rear axle was mounted upside down the pinion would be close. Is that possible?
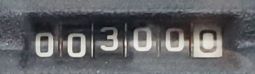 .150 Stroked Y-Block:327.25 ci @ >1hp per ci
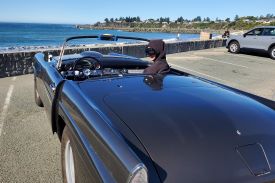
|
|
|
55blacktie
|
|
Group: Forum Members
Last Active: 13 hours ago
Posts: 1.2K,
Visits: 1.7K
|
Is your new 9" from a 57 T-bird? The 55-57 T-bird spring perches are taller than non-Bird axle housings, thereby dropping the rear ride height approximately 2". If you do not have the original spring perches, it could put your driveline angle outside acceptable limits.
|
|
|
55blacktie
|
|
Group: Forum Members
Last Active: 13 hours ago
Posts: 1.2K,
Visits: 1.7K
|
Sorry, I meant the spring perches lower the ride height about 2". The perches are taller, but being located under the axle housing, they actually lower the ride height.
|
|
|
DryLakesRacer
|
|
Group: Forum Members
Last Active: Last Year
Posts: 1.7K,
Visits: 340.0K
|
Open You Tube and go to “Larry Shaw Modified Suspension” and move the time to 1.55 and watch the movement using a 9” Ford rear..... I believe your all over thinking this. A u-joint can perform over a 22* movement, that’s 11 up and 11 down. Not that we would ever do or abuse them in such a manner.
We use leaf springs in our 1/2 mile dirt car with a slider and a shackle and in 7 years never had a problem with just normal greasing..
56 Vic, B'Ville 200 MPH Club Member, So Cal.
|
|
|
Brent
|
|
Group: Forum Members
Last Active: 5 Months Ago
Posts: 142,
Visits: 1.5K
|
The perch pad was a good question, I did use blocks to adjust the axle ride height. Larry Shaw Modified Rear Suspension 4-link POV - Bing videoI'm feeling lots better after watching the video, thanks! The pinion operation angle is all over the place and at full throttle. I think the early Birds were designed with the u-joints at high angles, I wish I had paid attention before taking it apart. I am hoping to hear how Vic Correnti has his Bird set up. He gets the front wheels off the ground. I can't imagine a way, without serious modifications, to reduce the angle to within the textbook specs. I do like to play outside of the box, and I do tend to overthink things before crossing the line. Thanks again...
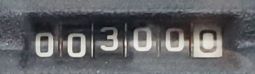 .150 Stroked Y-Block:327.25 ci @ >1hp per ci
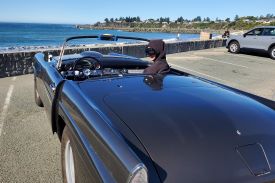
|
|
|
2721955meteor
|
|
Group: Forum Members
Last Active: Last Year
Posts: 927,
Visits: 190.0K
|
the dana book claims as long as the face angle on trans output is within 15 degrees of face angle input of the diff you will be ok the trans can be higher as long as the diff flanges are parallel to the trans flanges.,meaning the pinion can be off centre to the trans, the limit there is as long asujoint crosses don't rub. ther is a magnetic degree tool works well, they are made of plastic with magnet glued to hold them in place. the 15dgs is the max, and should be with the truck on the ground . and the spring bushings on the anchor end tight (no slop)
|
|
|